Teil 2: Herstellung eines Carbon-Heckrohrs
GfK und CfK – worin unterscheiden sich die Faserverbundwerkstoffe und wie lassen sie sich verarbeiten? Dieser Frage ging Dr. Klaus Huber im ersten Teil seiner Grundlagenserie nach. Nun geht es weiter mit der Herstellung von CfK-Rohren. Wie man dabei am besten vorgeht, erklärt er im folgenden Teil.
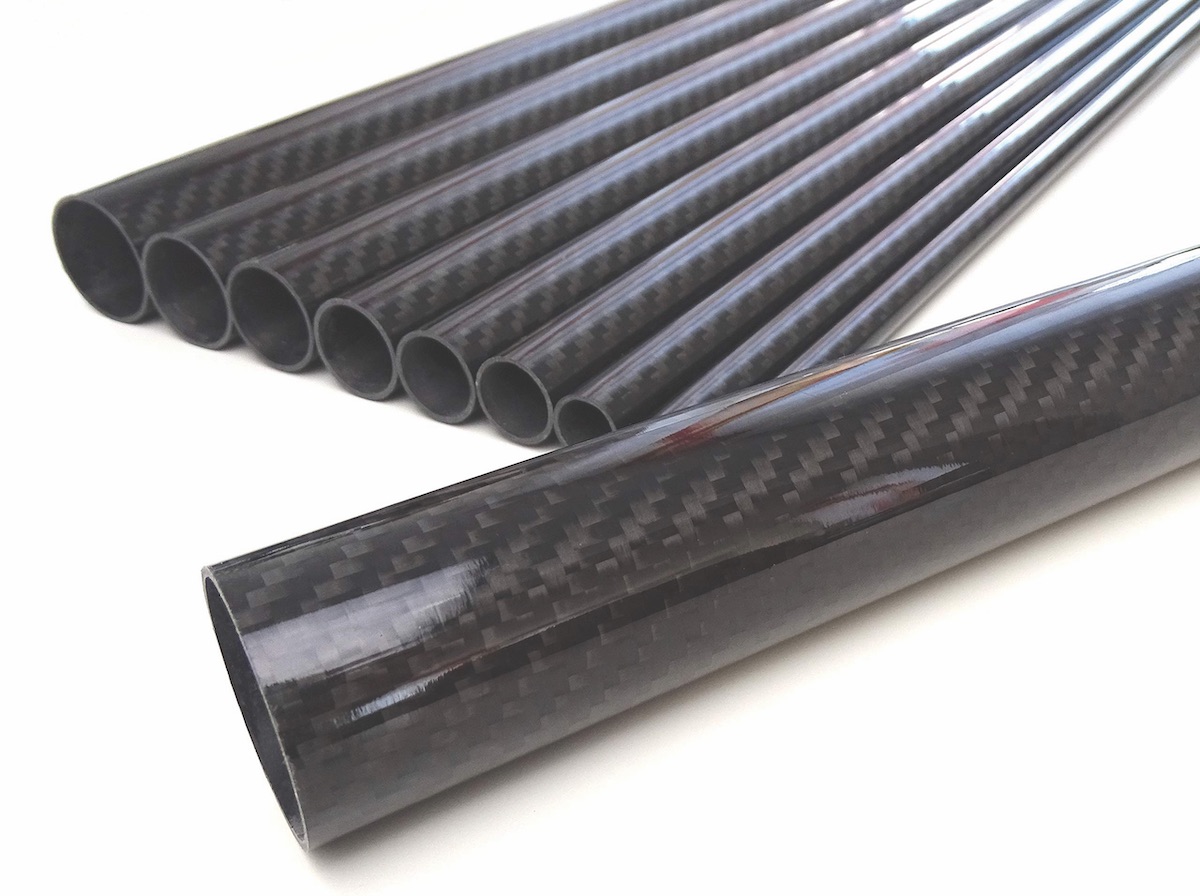
Zur Herstellung von Carbon-Rohren gibt es verschiedene Fertigungsverfahren. Man kann Rohre aus Carbon-Rowings oder Carbongewebe wickeln oder noch besser geflochtene Carbon-Schläuche über einen Wickelstab ziehen. Diese Schläuche lassen sich durch Ziehen oder Stauchen dem Durchmesser anpassen. Als Wickelstab eignen sich am besten Metallrohre in der richtigen Dimension.
So ein Metallrohr wird am besten mit wenigen Lagen Frischhaltefolie umwickelt und mehrmals mit Trennspray vorbehandelt. Nach dem Aushärten der Gewebelagen lässt sich der Stab durch die Frischhaltefolie leichter aus dem Rohr herausdrehen.
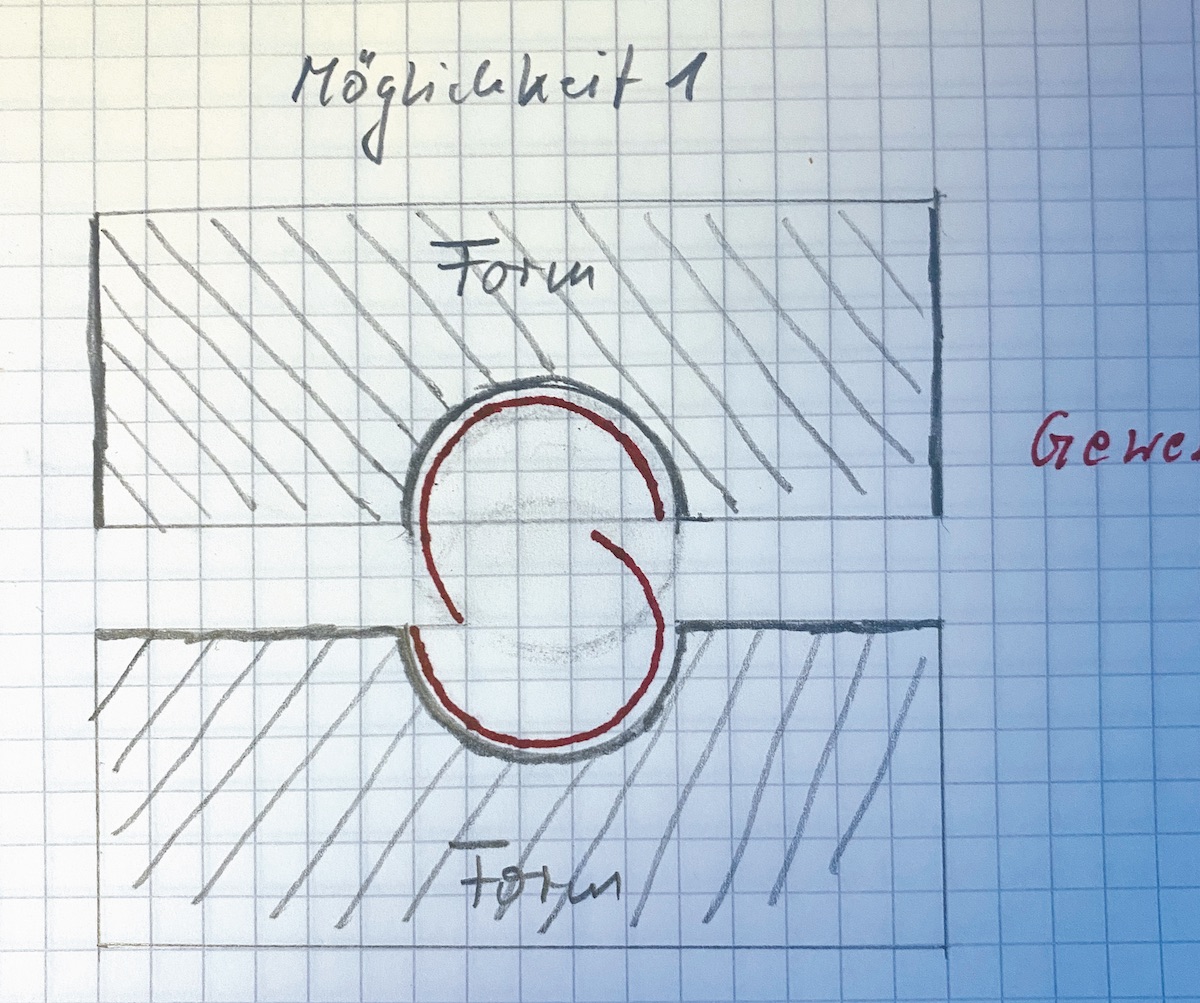
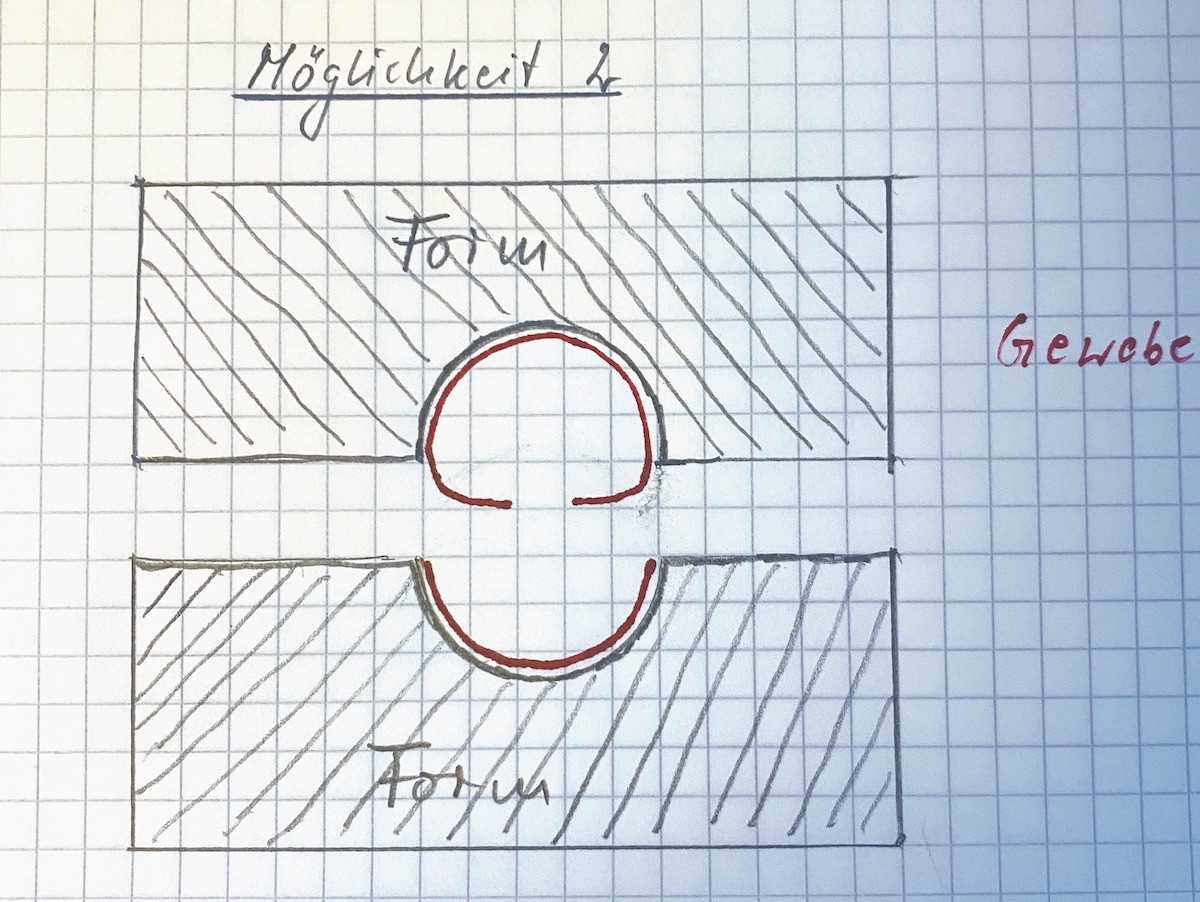
Wenn das Rohr eine sehr gute Oberfläche haben soll, einfach einen Schrumpfschlauch über das Rohr ziehen, was eine spiegelglatte Oberfläche ergibt. Um den Schrumpfschlauch über die Laminate ziehen zu können, unbedingt vorher den Carbonschlauch mit Tesakrepp sichern. Nachteil dieses Verfahrens ist aber der nicht eindeutige Außendurchmesser, was natürlich für ein Heckrohr essenziell wichtig ist.
Eine Variante dieses Wickelverfahrens ist das sogenannte Prepreg-Wickelverfahren, das hauptsächlich bei der industriellen Rohr-Fertigung angewandt wird. Prepregs sind Carbonverstärkungsfasern, die bereits mit Harz vorimprägniert sind. Als Matrix werden speziell modifizierte Epoxidharze (ggf. auch Phenolharze) verwendet, die bei Raumtemperatur nicht fließen. Unter Pressdruck (im Werkzeug oder Vakuum) und Temperatur verflüssigt sich das Harz für kurze Zeit und der Prepregstapel wird weich und verschiebbar, sodass auch komplizierte Formgebungen möglich sind. Nach kurzer Zeit härtet das Harz im Temperofen aus.
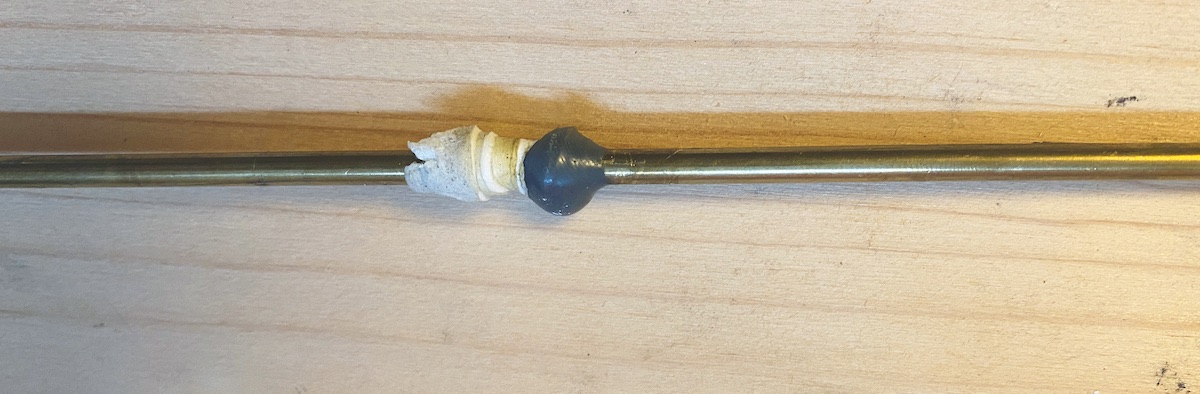
Für unsere Zwecke ist das Schlauchblasverfahren zu favorisieren. Hierbei kommen zweiteilige Negativformen zum Einsatz, in denen sich die Außenseite des Rohres abformt. Diese Rohre kommen fix und fertig aus den Formen mit einem sehr genau tolerierten Außendurchmesser, der durch die Negativformen vorgegeben wird. Aufgrund des hohen Druckes durch den aufblasbaren Schlauch während des Aushärteprozesses bekommt das Rohr eine höhere Steifigkeit und Festigkeit aufgrund des höheren Faseranteils bei gleichzeitig geringerem Gewicht.
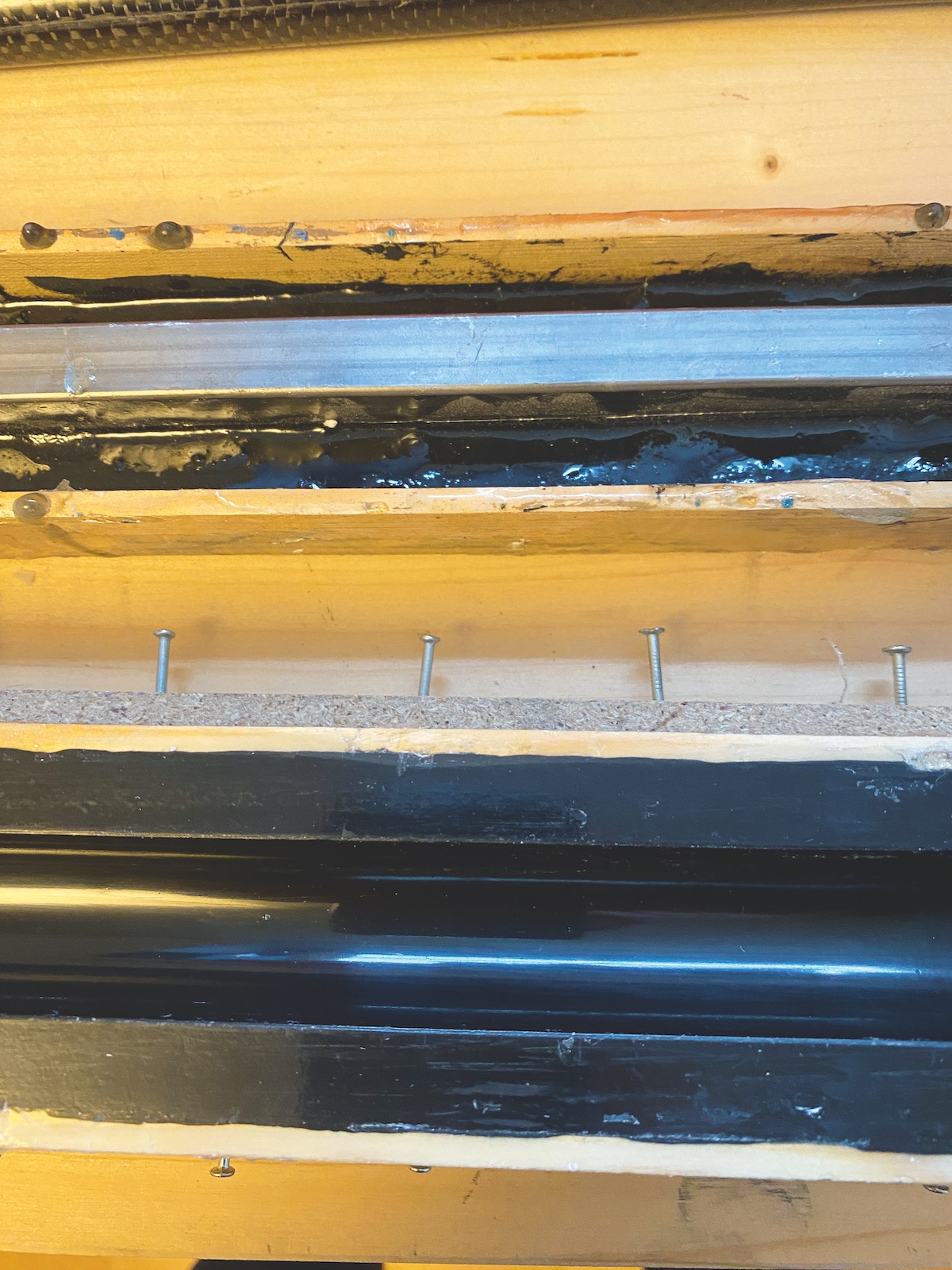
Als Urmodell für die Herstellung der Negativformen eignet sich ein Aluminiumrohr in dem gewünschten Außendurchmesser, was am besten auf Hochglanz poliert wird. Nebeneffekt ist, dass sich der Außendurchmesser durch die Politur um ca. 0,1–0,2 Millimeter reduziert, was für die Fertigung des späteren Carbonrohres eher von Vorteil ist.
Bei der Herstellung der Negativformen muss unbedingt ein Stahlprofil eingearbeitet werden, da die Formen innen mit dem oben erwähnten Schlauch mit 2 Bar aufgeblasen werden. Bei meinen Formen habe ich leider nur ein Stahlvierkantrohr mit 16 × 16 mm eingearbeitet, was viel zu schwach bemessen ist, besser wäre ein Stahlvierkantrohr von 30 × 20 mm oder 40 × 20 mm, am besten noch mit einem Alu-Rahmen.
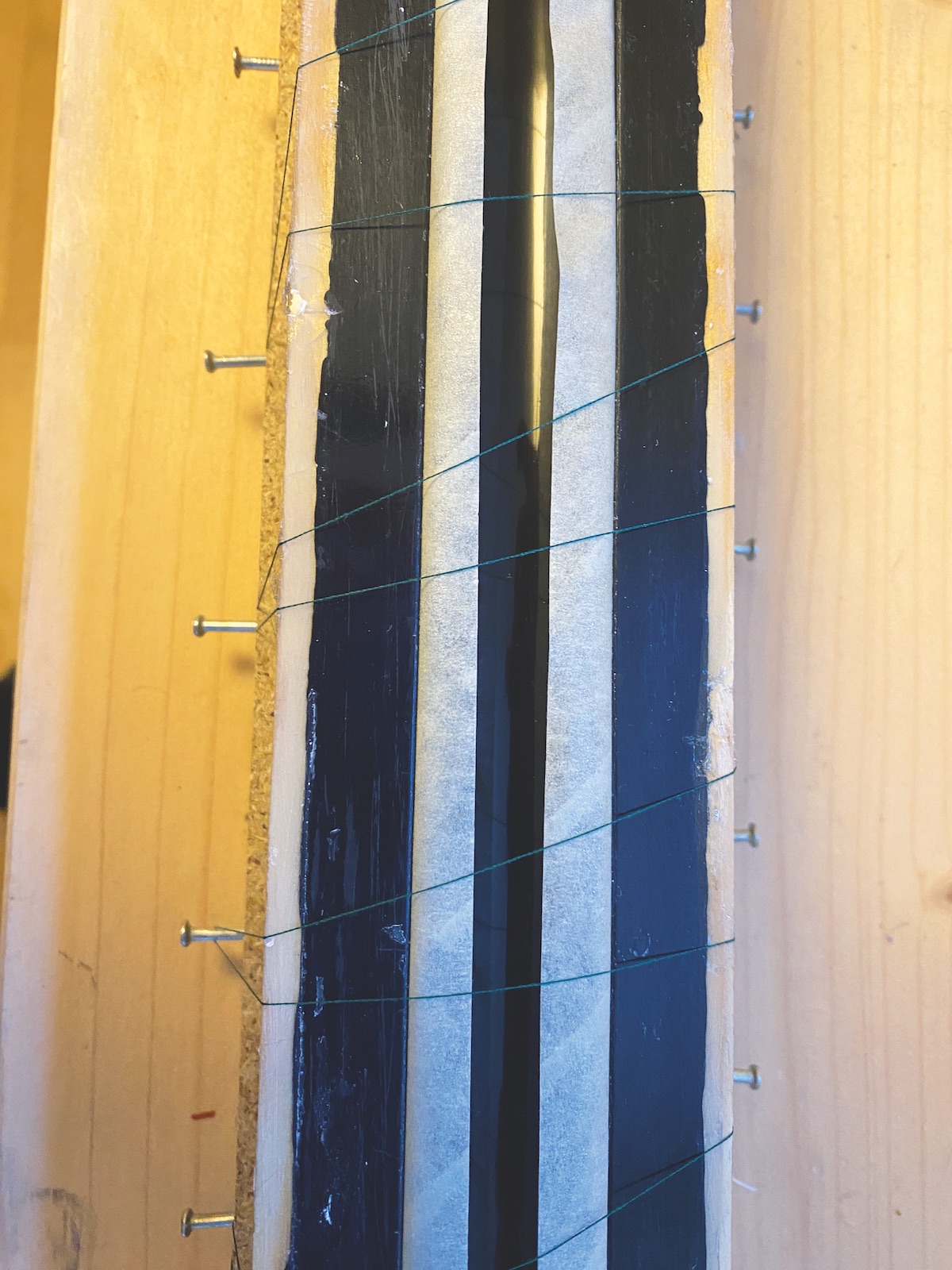
Das Finden eines geeigneten Schlauches zum Aufblasen der Formen kann sich durchaus schwierig gestalten. Nach unzähligen Versuchen mit diversen Modellierballonen verwende ich nunmehr einen immens dehnbaren Flex-Gartenschlauch. Dieser Schlauch ist so gut wie nicht zu zerstören. Als »Lanze« zum Aufziehen des Schlauchs eignet sich ein …
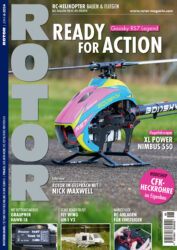
⇢ Den vollständigen Bericht lesen Sie in Ausgabe 6/2024. Ausgabe bestellen.