Teil 2: Rumpfbau und Scale-Details
Die Rumpffolien für den Airbus H160-Rumpfbausatz sind eingetroffen. Heli-Scale-Quality hat sauber gearbeitet und alle Unregelmäßigkeiten an den Formen beseitigt. Im Lieferumfang sind nun die Rumpffolien, die Folien für den Innenausbau und die Anbauteile enthalten. Einige der Anbauteile wurden wieder von Peter Reinerth selbst hergestellt. Der Bausatz ist also sehr umfangreich und wartet nun auf den Zusammenbau. Wie dieser durchgeführt wurde, erklärt Peter Reinerth im Folgenden.
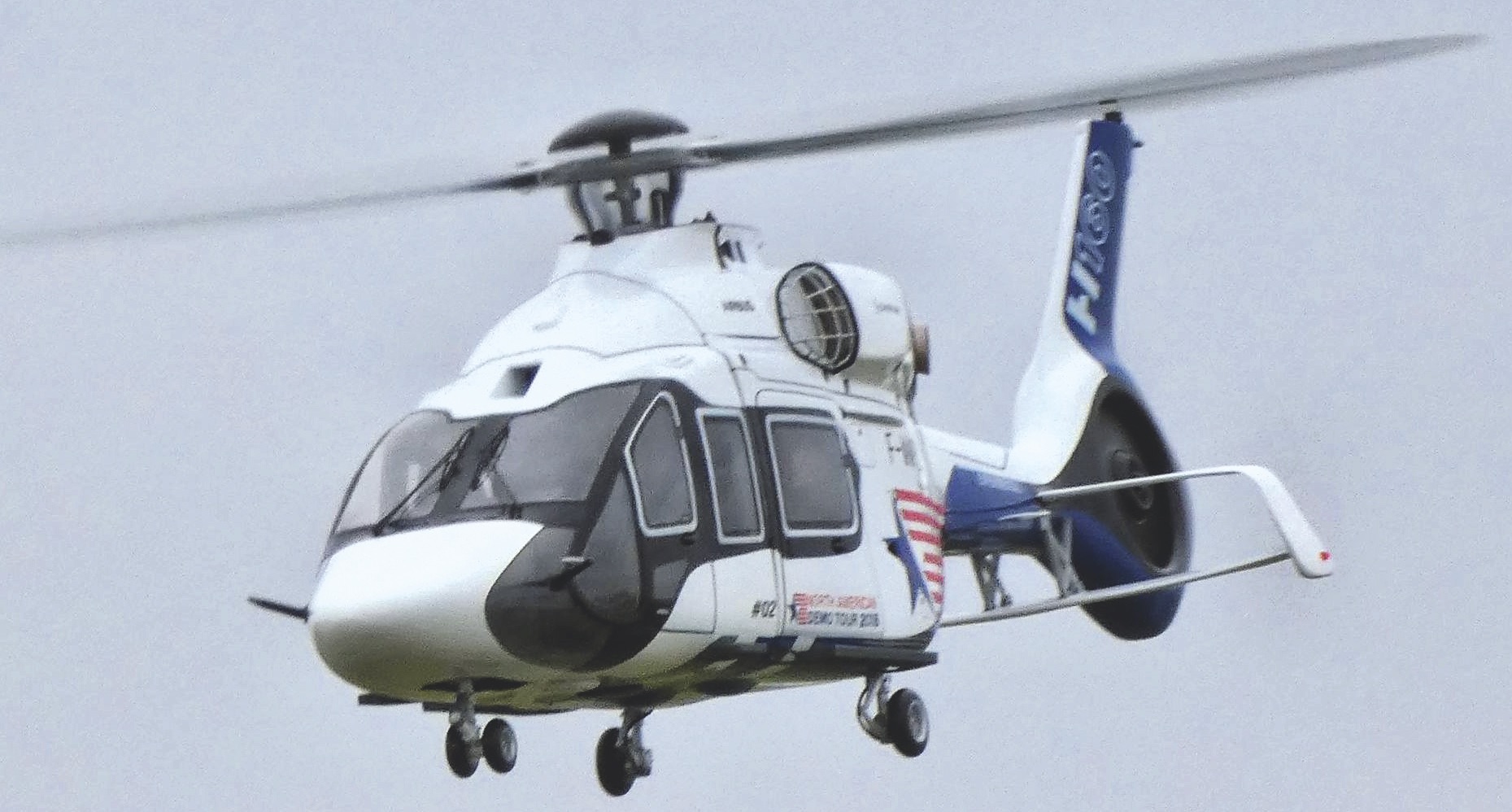
ZUSAMMENBAU DES
RUMPFS und des HECKs
Ich beginne am Heck und führe die Hälften oberhalb des Fenestron zusammen. Hier ist der richtige Zuschnitt wichtig, um spätere Korrekturen zu vermeiden. Nach dem Zuschneiden sieht man, dass die Teile am Heck kaum einen Verbindungsstreifenrand haben. Folienteile, die fast flach sind, werden ohne Verbindungsstreifen verklebt. Ein Tropfen flüssiger Sekundenkleber, den man innen an der Kante entlang laufen lässt, verklebt die Hälften.
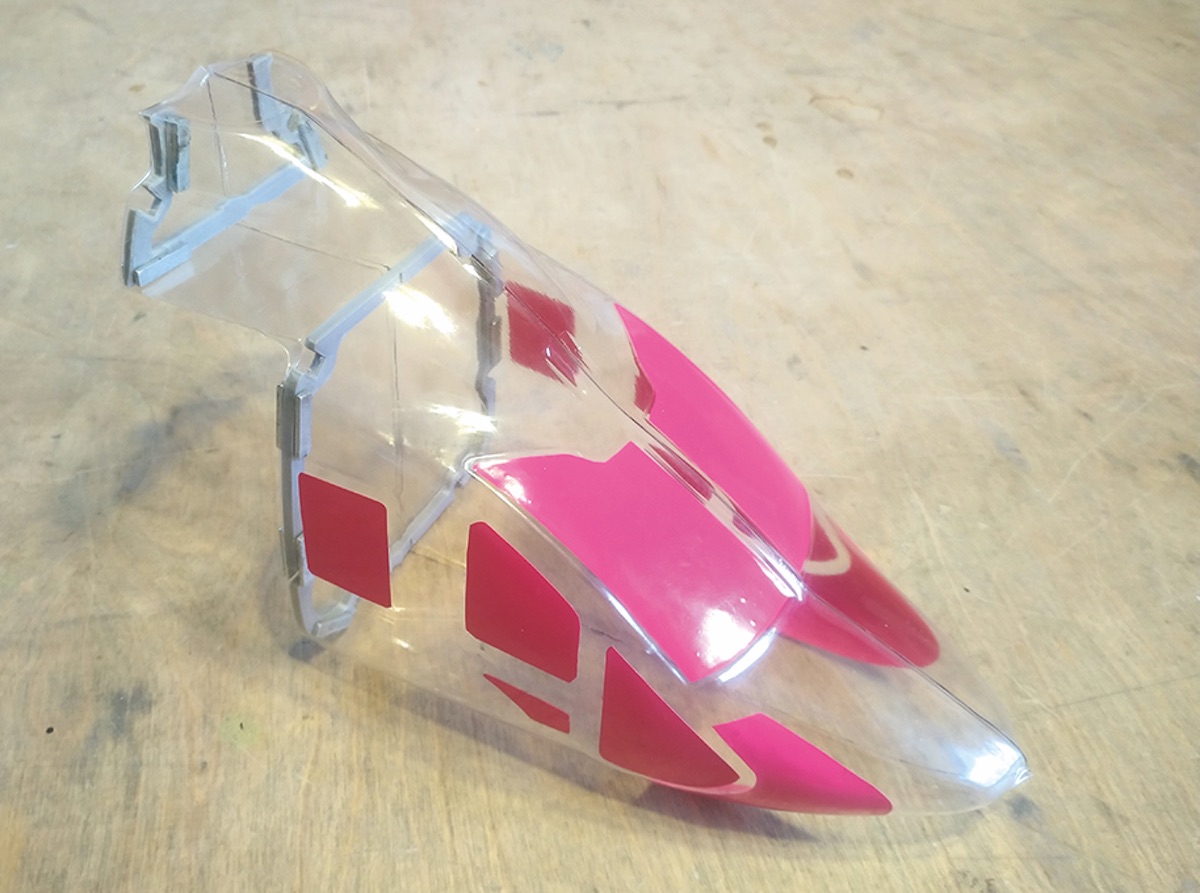
Der untere Teil des Hecks ist stark gebogen. Hier ist ein gerader Verbindungsstreifen ungeeignet, darum wird der Streifen mehrfach eingeschnitten, um ihn über zwei Ebenen wölben zu können. Die Fläche, die mit dem Heckausleger verbunden wird, verstärke ich mit Folienwinkeln. Auch den Heckausleger verstärke ich nach dem Zusammenkleben der Hälften.
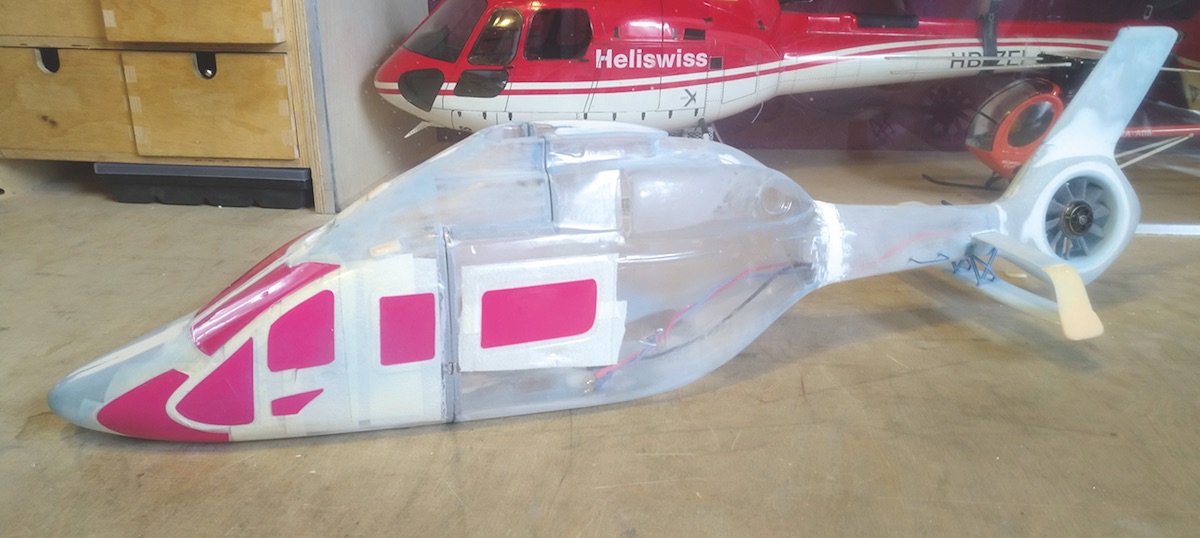
Das Leitwerk des H160 besteht aus zwei Tragflächen und jede der Tragflächen aus zwei Folien. Diese sind so flach, dass direkt in der Rundung zugeschnitten werden muss. Auch hier bleibt nur das Kleben ohne Verbindungsstreifen als einzige Möglichkeit. Der Ausschnitt für das Leitwerk ist am Ausleger markiert und kann richtig platziert werden. Die Außenteile für den Ausleger sind 3D-gedruckte Teile und werden in die Tragflächen eingeklebt. Da ich die Version des H160 baue, die als Demo-Maschine unterwegs war, habe ich die abweichende Form der Leitwerkstützen gezeichnet und gedruckt – diese werden hier eingesetzt. Für die später von Airbus ausgelieferte Version steht ein passendes Teil zur Verfügung.
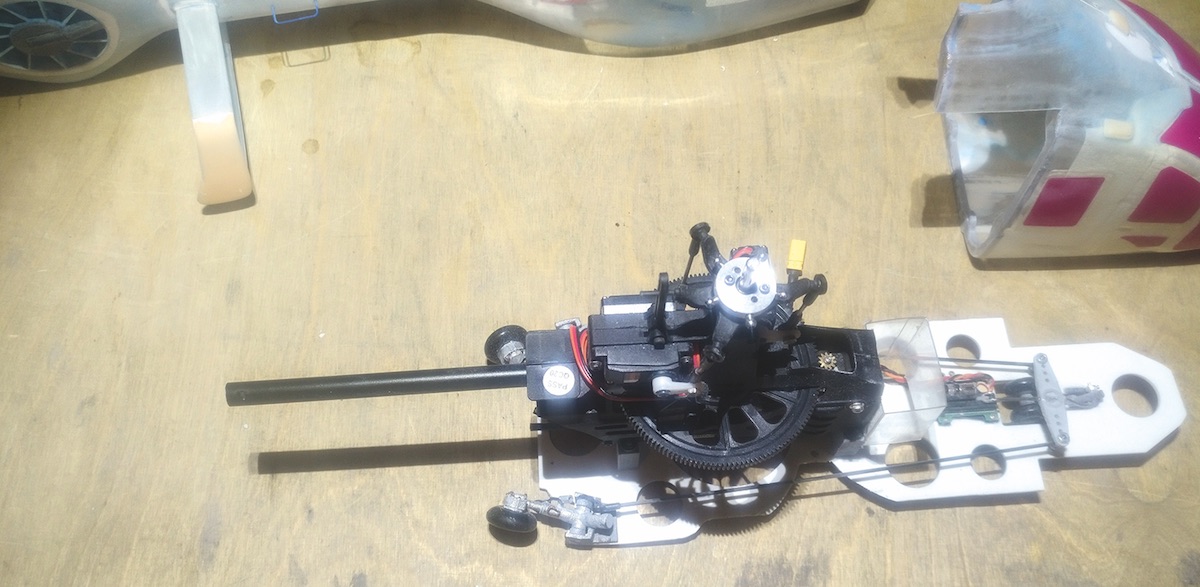
Der Motor-Stator für den Fenestron wird nun in seinen Impellermantel montiert und die Kabel in den Kabelschacht eingezogen. Anschließend schütze ich die Wicklungen und Kugellager mit einem Kreppband und klebe den Stator des Fenestrons ein. Die Kabel werden in den Ausleger eingezogen.
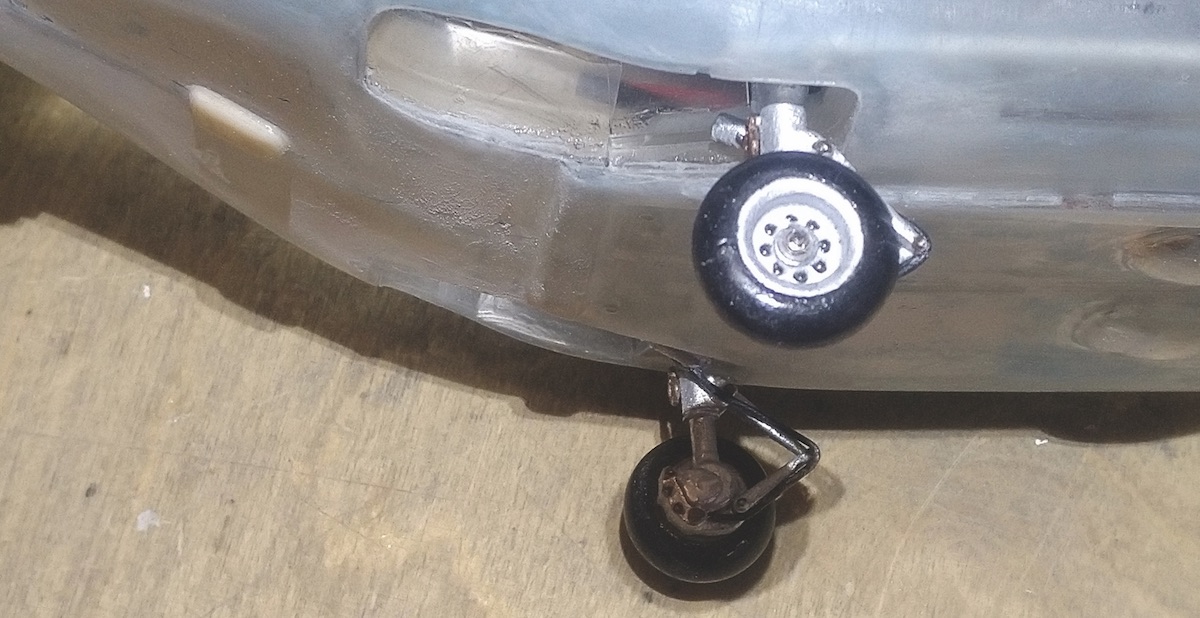
Alle Klebestellen der Folien werden mit Polyester-Feinspachtel gefüllt und geglättet. Auch der Übergang des Höhenleitwerks zum Fenestron-Gehäuse und das Gehäuse selbst werden mit Spachtelmasse geglättet – ebenso die Klebestellen des Höhenleitwerks. Nach dem Trocknen der Spachtelmasse schleife ich die Stellen glatt.
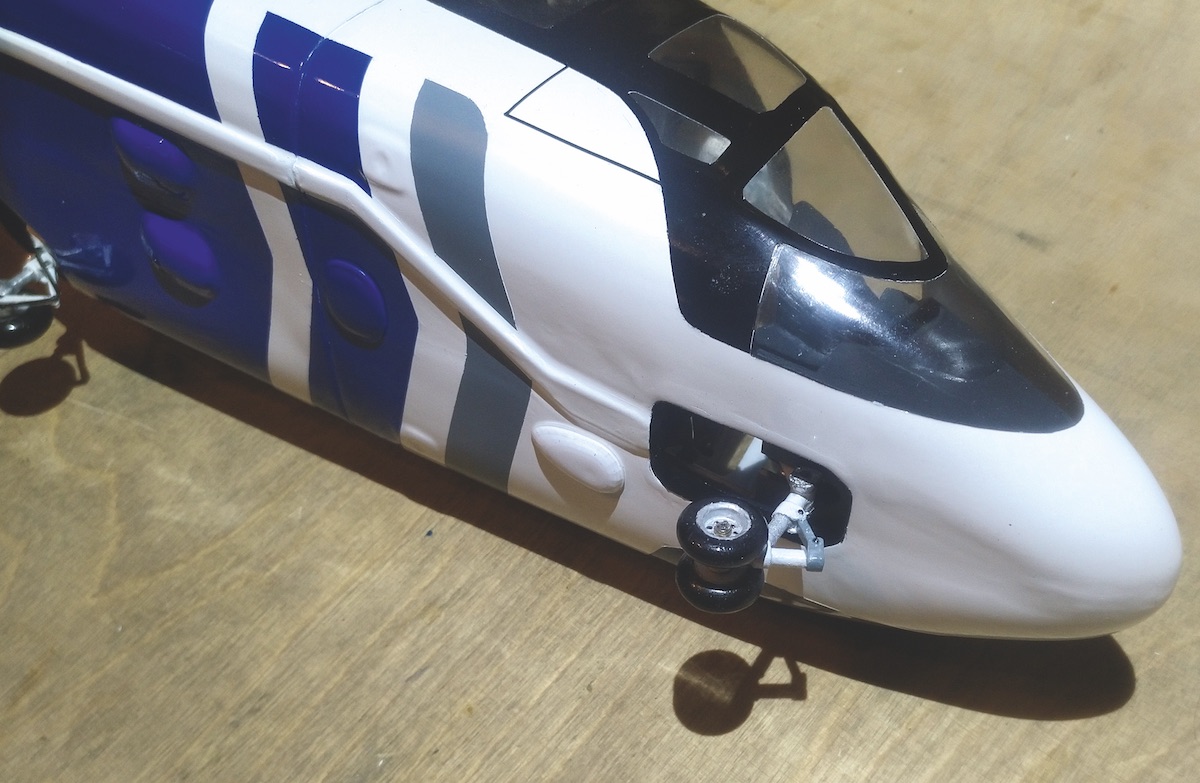
ZUSAMMENBAU DES RUMPFS UND KABINE
Im nächsten Schritt schneide ich die Maskierfolien für die Fenster nach den Schablonen zu und maskiere die Fenster innen und außen. Vor dem Ausschneiden überprüfe ich die Passung zum Ausleger. Im vorderen Bereich der Trennstelle des abnehmbaren Kabinenteils habe ich einen Spant gedruckt, der das Maß bestimmt. Nach diesen Kriterien schneide ich den Rumpf passend zu. Die großen Folienteile lassen sich bequem mit Verbindungsstreifen verkleben. Das gleiche gilt für den abnehmbaren Teil der Kabine: Fenster maskieren, Spanten zu Hilfe nehmen, um passend zuschneiden zu können, und nach dem Zuschneiden mit Verbindungsstreifen verkleben. Anschließend werden die …
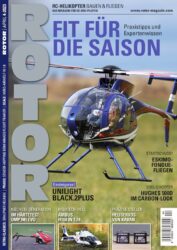
⇢ Den vollständigen Bericht lesen Sie in Ausgabe 4/2023. Ausgabe bestellen